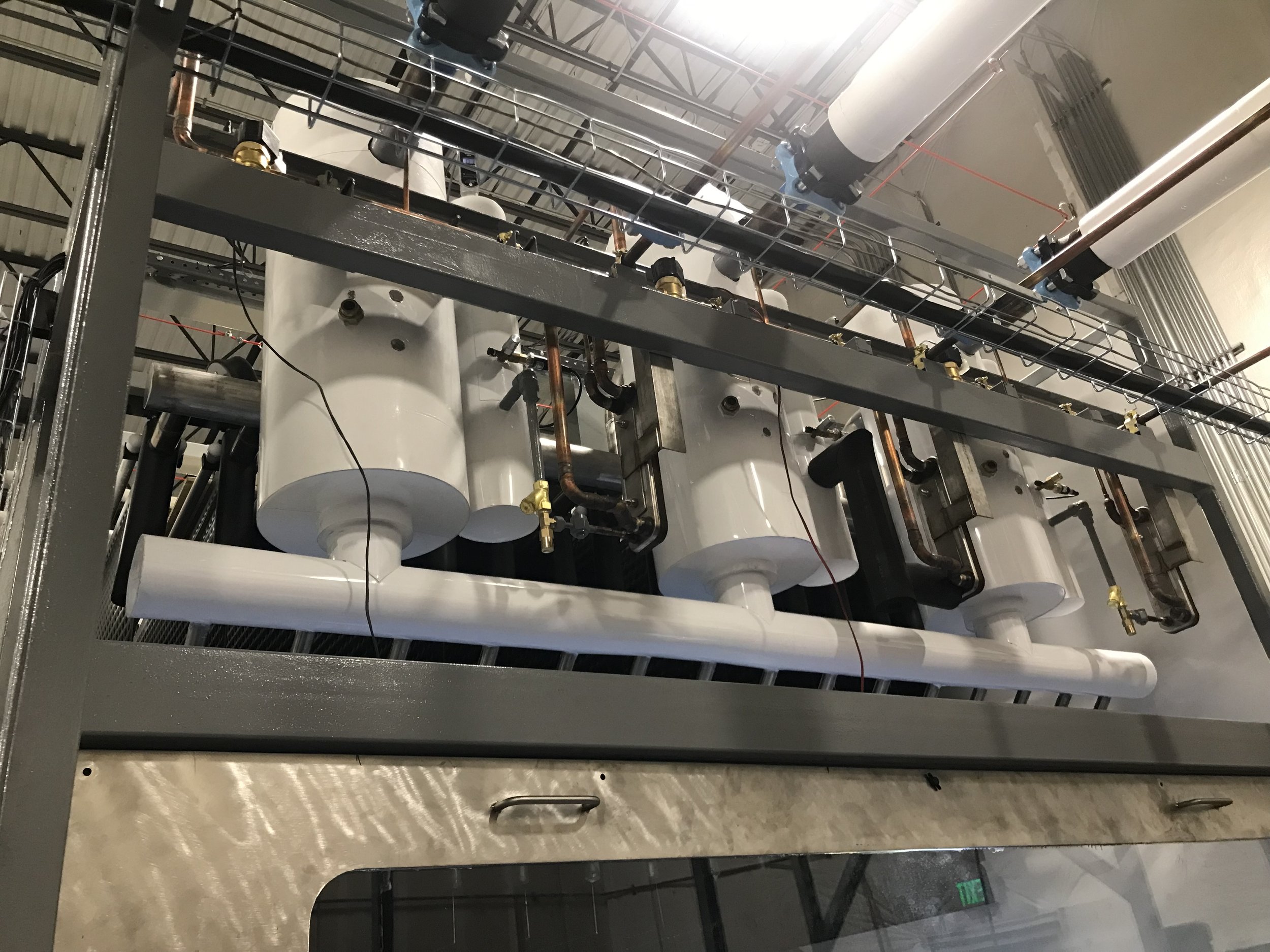
services
Our resourceful team of experts is ready to take on any challenge, no matter how complex.
preventative maintenance
For many companies, preventative maintenance is just something they offer lip service to. For us, it’s an important part of our work and is integral to the overall project quality. Those promises in our maintenance contracts? We stand by them.
We perform scheduled maintenance tasks per the needs of both the equipment and the customers. These tasks include things like filter and belt replacements, oil changes, cleaning heat exchangers, etc. We also set up contracts to perform regular, tailor-made inspections of refrigeration and HVAC equipment, and log data points for accuracy.
The intervals for maintenance and inspections vary from weekly to quarterly. These inspections help reduce downtime in production lines, reduce food waste from incorrect temperature food storage rooms and reduce maintenance and energy costs by catching problems early.
service calls
Our service work is second to none. We see our relationship with our customers as a partnership—we care deeply for their businesses and understand that there is a lot on the line if their mechanical systems do not function correctly.
Typically, our customers call us for a service call when they are alerted to an issue with one of their mechanical systems. This could be something like a high temperature alarm on a cooler, or an alarm from a refrigerant leak detector. Those types of alarms don’t always go off during business hours, but we respond to emergency calls 24/7, 365 days a year.
In addition to quick response times, we also serve our customers by keeping our service trucks fully equipped in terms of parts and tools. We understand that clients don’t have days to wait for a part to come in while their mechanical systems are down. That’s why we are always thinking ahead and planning ahead, bringing the parts, tools, and skills to repair the system as quickly as possible. You won’t have to wait long for a technician to show up and you won’t have to wait for materials to arrive.
An advantage of being in the business for as long as we have is the relationships we’ve developed with subcontractors. If a service call requires something more specialized than what we can do on the spot, we have a strong support network that we can tap into.
Installation
Installations typically occur when there is a new project or when a major piece of equipment needs to be replaced. Our philosophy is to prioritize quality over quantity. We use high-level technicians to manage our installations to ensure optimal performance, longer lifespans, and lower maintenance costs.
Our exceptional technical knowledge sets us apart from the competition and gives us the ability to deliver high quality installations. Have a challenging project? That’s where we really shine. Whether it’s a difficult installation or there are time constraints, we meet deadlines without sacrificing quality.